Directional solidification Contents Theory References Further reading Navigation menu10.1016/S0735-1933(01)00321-9Metal casting: a sand casting manual for the small foundry, Vol. IIScience and Engineering of Casting Solidificationee
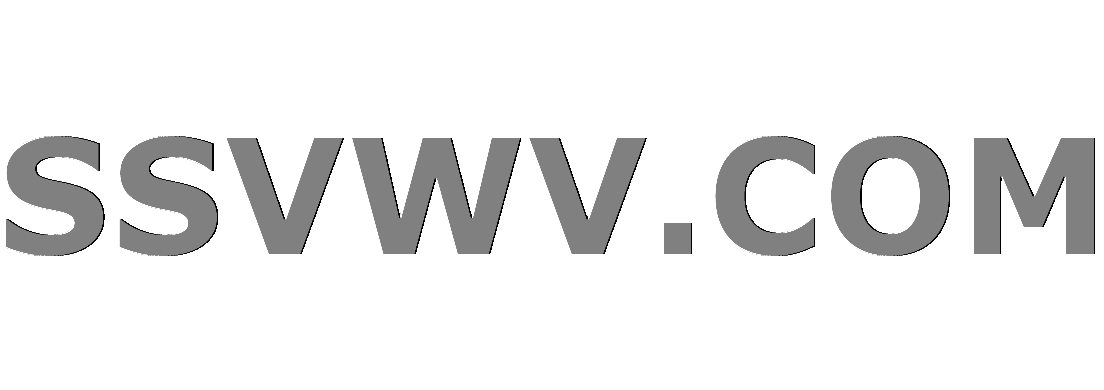
Multi tool use
CentrifugalContinuousDieEvaporative-patternFull moldLost foamInvestment (Lost wax)Permanent moldPlaster moldSandSemi-solid metalShaw processShell moldingSpinCasting defectsDraftDrossIngotSemi-finished casting productsSlag
Casting (manufacturing)
solidificationcastingsspruemetalsalloysshrinkpartition coefficientScheil equationzone meltingmulticrystallinesiliconsolar cells

Directional solidification

Progressive solidification
Directional solidification (DS) and progressive solidification are types of solidification within castings. Directional solidification is solidification that occurs from farthest end of the casting and works its way towards the sprue. Progressive solidification, also known as parallel solidification,[1] is solidification that starts at the walls of the casting and progresses perpendicularly from that surface.[2]
Contents
1 Theory
2 References
2.1 Bibliography
3 Further reading
Theory
Most metals and alloys shrink as the material changes from a liquid state to a solid state. Therefore, if liquid material is not available to compensate for this shrinkage a shrinkage defect forms.[3] When progressive solidification dominates over directional solidification a shrinkage defect will form.[2]

geometrical shape of the mold cavity has direct effect on progressive and directional solidification. At the end of tunnel-type geometries divergent heat flow occurs, which causes that area of the casting to cool faster than surrounding areas; this is called an end effect. Large cavities do not cool as quickly as surrounding areas because there is less heat flow; this is called a riser effect. Also note that corners can create divergent or convergent (also known as hot spots) heat flow areas.[4]
directional solidification chills, risers, insulating sleeves, control of pouring rate, and pouring temperature can be utilized.[5]
Directional solidification can be used as a purification process. Since most impurities will be more soluble in the liquid than in the solid phase during solidification, impurities will be "pushed" by the solidification front, causing much of the finished casting to have a lower concentration of impurities than the feedstock material, while the last solidified metal will be enriched with impurities. This last part of the metal can be scrapped or recycled. The suitability of directional solidification in removing a specific impurity from a certain metal depends on the partition coefficient of the impurity in the metal in question, as described by the Scheil equation. Directional solidification (in zone melting) is frequently employed as a purification step in the production of multicrystalline silicon for solar cells.[citation needed]
References
^ Stefanescu 2008, p. 67.
^ ab Chastain 2004, p. 104.
^ Kuznetsov, A.V.; Xiong, M. (2002). "Dependence of microporosity formation on the direction of solidification". International Communications in Heat and Mass Transfer. 29 (1): 25–34. doi:10.1016/S0735-1933(01)00321-9..mw-parser-output cite.citationfont-style:inherit.mw-parser-output .citation qquotes:"""""""'""'".mw-parser-output .citation .cs1-lock-free abackground:url("//upload.wikimedia.org/wikipedia/commons/thumb/6/65/Lock-green.svg/9px-Lock-green.svg.png")no-repeat;background-position:right .1em center.mw-parser-output .citation .cs1-lock-limited a,.mw-parser-output .citation .cs1-lock-registration abackground:url("//upload.wikimedia.org/wikipedia/commons/thumb/d/d6/Lock-gray-alt-2.svg/9px-Lock-gray-alt-2.svg.png")no-repeat;background-position:right .1em center.mw-parser-output .citation .cs1-lock-subscription abackground:url("//upload.wikimedia.org/wikipedia/commons/thumb/a/aa/Lock-red-alt-2.svg/9px-Lock-red-alt-2.svg.png")no-repeat;background-position:right .1em center.mw-parser-output .cs1-subscription,.mw-parser-output .cs1-registrationcolor:#555.mw-parser-output .cs1-subscription span,.mw-parser-output .cs1-registration spanborder-bottom:1px dotted;cursor:help.mw-parser-output .cs1-ws-icon abackground:url("//upload.wikimedia.org/wikipedia/commons/thumb/4/4c/Wikisource-logo.svg/12px-Wikisource-logo.svg.png")no-repeat;background-position:right .1em center.mw-parser-output code.cs1-codecolor:inherit;background:inherit;border:inherit;padding:inherit.mw-parser-output .cs1-hidden-errordisplay:none;font-size:100%.mw-parser-output .cs1-visible-errorfont-size:100%.mw-parser-output .cs1-maintdisplay:none;color:#33aa33;margin-left:0.3em.mw-parser-output .cs1-subscription,.mw-parser-output .cs1-registration,.mw-parser-output .cs1-formatfont-size:95%.mw-parser-output .cs1-kern-left,.mw-parser-output .cs1-kern-wl-leftpadding-left:0.2em.mw-parser-output .cs1-kern-right,.mw-parser-output .cs1-kern-wl-rightpadding-right:0.2em
^ Stefanescu 2008, p. 68.
^ Chastain 2004, pp. 104–105,..
Bibliography
Chastain, Stephen (2004), Metal casting: a sand casting manual for the small foundry, Vol. II, 4, Stephen Chastain, ISBN 978-0-9702203-3-2.
Stefanescu, Doru Michael (2008), Science and Engineering of Casting Solidification (2nd ed.), Springer, ISBN 978-0-387-74609-8.
Further reading
Campbell, John, Castings (2nd ed.), Butterworth-Heinemann, ISBN 0-7506-4790-6.
Wlodawer, Robert (1966), Directional solidification of steel castings, Pergamon Press.
4kXcmT9H5cRfm EXJKFmrFwgStO 4Mo33e2LxcRaQRiwGr9uFdTgAgt1B2,7KhuqojzJ1 WaZZjsMZ5 ku1Xv9F8zCdeNLSb,vI